We need batteries in every aspect of our life, from phones, laptops, tablets, cameras, to scooters and electric cars.
Lithium-ion batteries have always been an Asian-centric industry since the beginning. It was first commercialised by Japanese company Sony for its video cameras and Walkman media players. Since then, Panasonic, LG, Samsung and SK have took lead in producing Lithium-ion batteries for various portable devices including smart phones and laptops.
The demand for Lithium-ion batteries has risen sharply in the past five years and is expected to grow from 44.2 billion dollars in 2020 to 94.4 billion by 2025, mostly due to electric vehicles.1 EVs are expected to hit 10% of global passenger vehicle sales by 2025, rising to 58% of sales by 2040.2
China sold roughly one million more EVs than the U.S. in 2020. Market forecasts show that EV sales will eclipse combustion engine vehicle sales in the next 15 years. But this requires battery breakthroughs. China currently has nearly 100 large-scale battery manufacturing plants, while the U.S. has just 4, and none of them are American owned.3
It’s hard to image that the U.S. would allow itself to rely on China or any other countries for battery suppliers, especially for EVs. But how can U.S. catch up in this competition? How can the world’s battery industry evolve to support the growing EV demand? Let’s explore some possibilities together.
Policies to Push Mining and Manufacturing
The batteries are made up of a mix of metals and minerals, including nickel, cobalt, lithium, graphite and cooper that come from all over the world. These materials are usually minded in Australia, South America, Africa, China, and Indonesia, and then sent to China for refining and finally to the battery makers.
With the government’s big EV push, China has now become the world’s largest Lithium-ion battery supplier, handling 80% of the world’s raw mineral refining, 77% of the world’s battery cell manufacturing and 60% of the world’s battery component manufacturing.4
In fact, the problem of America is not a lack of resources. The U.S. Geological survey reports that the U.S. actually has more lithium reserves than China but the mines just haven’t been built yet. That’s because until recently, domestic automakers haven’t really committed to EVs and the policies weren’t there to support.
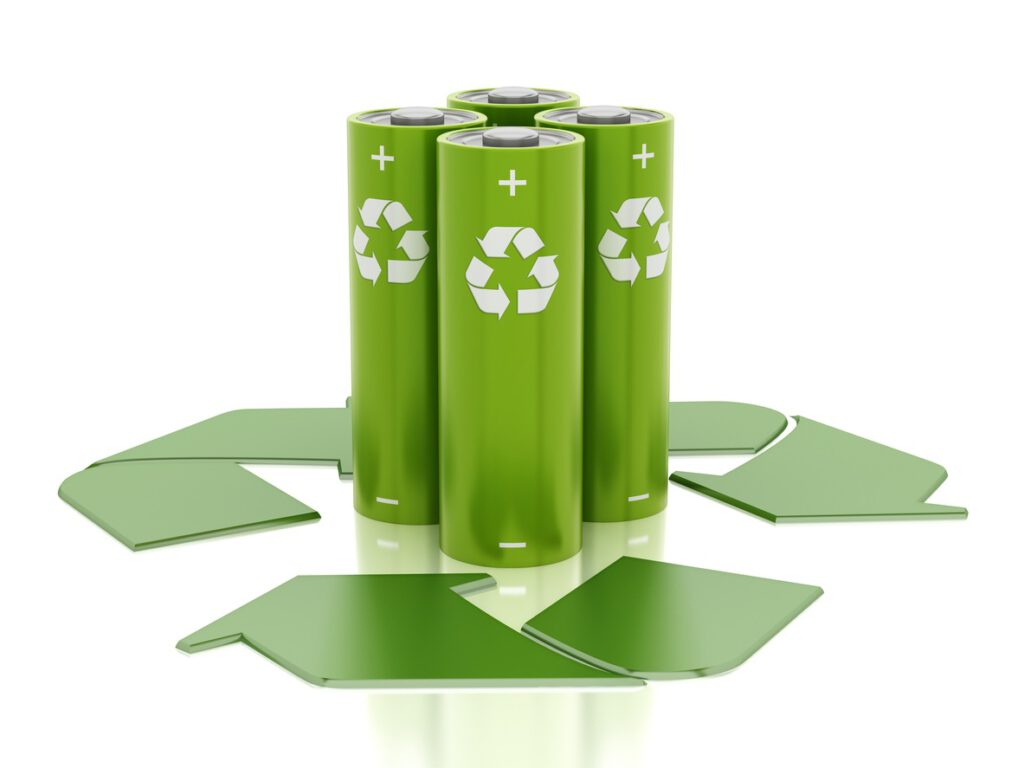
Source: bike-eu.com
But now the government has realised that the batteries and lithium and other raw materials components are as important as oil. Investors follow the source of the value chain and make investment in new mines, refineries and recyclers.
Experts indicate that the U.S. needs to build out a domestic supply chain that starts with mining of raw materials in the country and ends with getting the battery giants to set uplocal manufacturing facilities.
However,it takes a lot of effort to get the metals out of the ground. Even if major players all start to plan facilities today, the country would probably still face a temporary shortage. It requires time to acquire the land, get all the environmental permits, and finish the construction to make the facilities operate.
On the other hand, domestic automakers are also getting serious about going electric finally. GM plans to be fully electric by 2035, and be carbon neutral by 2040.5
To achieve these goals, car manufacturers may need more innovative solutions apart from digging mines and building battery factories from scratch.
Material Technology to Extend Battery Performances and Lifecycle
The batteries are the most expensive part of an electric car. Although the cost of EV is dropping, it’s still dominated by the cost of the battery. And within the battery, the biggest cost are the materials.
Meanwhile, poor battery performance is directly linked to consumer range anxiety and the high price of EV ownership.
The way to further reduce the cost of EVs and enhance the user experience is to figure out how we make the most out of each battery produced, and extend the battery lifecycle as long as possible.
That’s where we need material science and technology to help. By being able to control the flow of ions in the battery while charging and discharging a battery, scientist can change all sorts of aspects of a battery, including energy density, to longevity.
Some of the nanoscale battery technology can help to reduce the amount of cobalt needed in the cathode of lithium-ion battery. Adopting such technology can save money and eliminate one of the raw material supply chain concerns we mentioned earlier for lithium-ion batteries.
By coating a micron thick layer of proprietary polymer membrane onto existing battery separators, and swapping a lithium metal anode for graphite to deliver a roll-to-roll scalable product, such technology can increase the energy density of a battery by 30% at a competitive price.
The only challenge for such technology to be adopted into EVs is the slow technology validation cycle of the existing automotive industry. However, from an ESG point of view, such innovation technology can play a key role in reducing the total amount of battery production for EVs. Despite being overall positive in total CO2 equivalent emission, EV battery production is generating a substantial amount of emissions, which reduces the total positive number to the environment. Therefore, such initiatives are definitely worth paying attention to in the near future.
Recycling Technology to Reuse Critical Materials
Another approach to solve the shortage of battery is to look at the recycling end.
As we already know, the whole mining and manufacturing process of the battery packs accounts for the biggest source of CO2 emission in making electric vehicles. By the end of the life cycle, the batteries can’t end up in landfills because they are flammable and toxic. According to Greenpeace, a total of 7.05 million tonnes of EV lithium-ion batteries are expected to go offline between 2021 and 2030.6
Wouldn’t it be wonderful if we can recycle raw materials from battery waste, so that we could help solve the problem of raw material shortage, meanwhile saving the planet from those toxic waste?
The good news is that these old batteries are still filled with materials that are good as new. That means the critical materials inside them are highly recyclable. Industrial pioneers can now recover 95% to 98% of many of those critical materials like nickel, cobalt and copper. And all of these metals are able to go back straight into reuse again and again.7
For example, Redwood Materials is already recycling tons of batteries and sending some of the recovered materials to the battery makers to put them back into EVs.8
However, the bad news is that this technology is too expensive. It still requires effort from all parties, including consumers, to help make recycle possible.
But again from an ESG point of view, we do believe that one day recycling is going to be a strong factor to help EVs achieve carbon neutrality. Battery manufacturers need to take advantage of the capacity of older cells to create the next generation batteries out from recycling.
2https://www.cnbc.com/2021/04/10/tesla-jb-straubel-redwood-materials-battery-recycling.html
3 https://www.cnbc.com/2021/04/10/tesla-jb-straubel-redwood-materials-battery-recycling.html
5 Source: MarketsandMarkets
6 Source: BloombergNEF
7 https://www.cnbc.com/2021/04/08/the-us-is-facing-a-lithium-ion-battery-shortage-with-ev-growth.html
8 Source: BloombergNEF
Reference:
https://www.cnbc.com/2021/04/08/the-us-is-facing-a-lithium-ion-battery-shortage-with-ev-growth.html
https://www.cnbc.com/2021/04/10/tesla-jb-straubel-redwood-materials-battery-recycling.html
.
.