(Picture: unsplash.com)
Did you know that cement is a major source of carbon emission?
Every year, the production of cement accounts for 8 percent of global CO2 emissions. If the cement industry were a country, it would be the world’s third-largest emitter of CO2.
Cement is the glue that holds concrete together, and concrete is the second most consumed material on the planet after water. It is used to build our roads, bridges, sidewalks, airports, all kinds of buildings including skyscrapers. It is the foundation of modern civilization.
Given this common construction material can be moulded into nearly any shape, it has inspired architects from Le Corbusier to Ando Tadao to create extraordinary concrete buildings around the world.
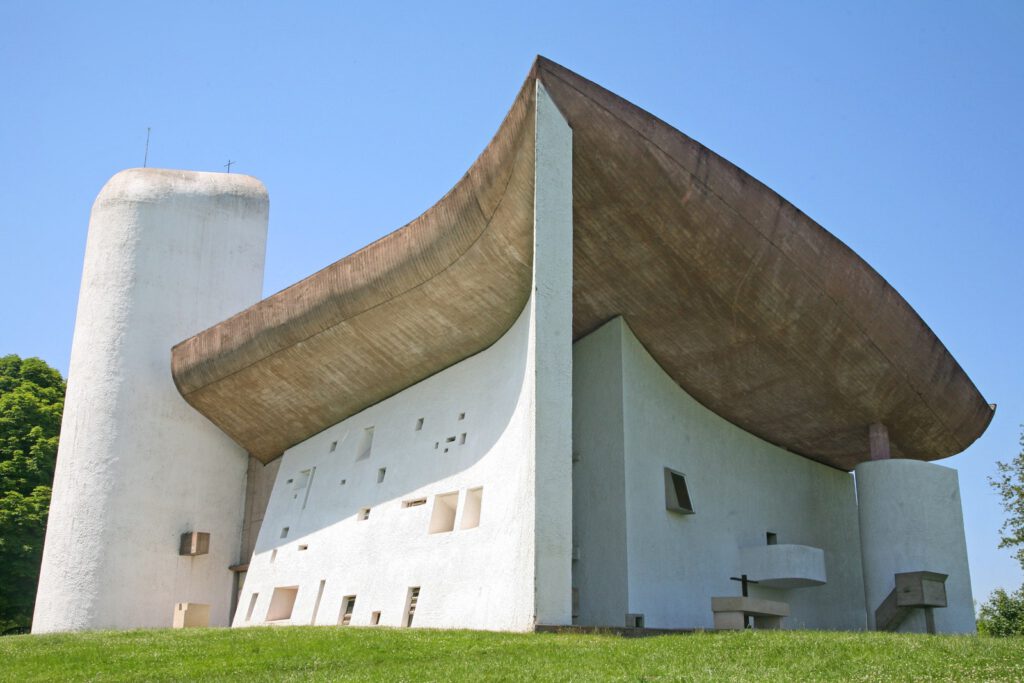
Notre Dame du Haut by Le Corbusier
Completed in 1955, Listed as UNESCO Wolrd Heritage in 2016
photo credit : Architectural Digest
The global demand for housing is rising, especially in developing countries. The world is expected to add more than two trillion square feet of new building space by 2060. That’s the equivalent of adding another New York City every month for the next 40 years.
How can we keep up with the speed of development while taking good care of the blue planet?
Some companies and institutions have come up with innovative solutions to reduce cement’s carbon footprint, while other inventors are trying to develop cement-free concrete. How are these initiatives going so far? Let’s take a look together.
CARBON CAPTURE
The production of cement involves an energy intensive process.
“The way you generally make cement is you mine limestone from earth and then you mix it with some other things, and heat it up in a very high temperature about 1,500 ℃. Then there’s a chemical transformation that takes place, and there’s CO2 from emitted as part of the chemical transformation, as well as from heating cement kilns to extremely high temperatures.” explains Jeremy Gregory, Executive Director from MIT Concrete Sustainability Hub.
One solution for reducing carbon footprint of cement is to trap the CO2 emissions in concrete. One Canadian company, Carbon Cure, has developed a technology that bolts onto an existing concrete plant, injects CO2 into concrete while it’s being mixed. When the concrete hardens, CO2 is convert to mineral, and gets trapped in the concrete permanently. And the best things is adding CO2 actually makes concrete stronger, and requires less cement in the mix.
Companies have to pay to use Carbon Cure system and to buy CO2 from the factory where it’s emitted, but they save money by using less of the most expensive ingredient, cement. Although the costs would equal themselves out, it’s still going to take the whole concrete industry changing the way they do things.
ALTERED MIXTURE
Solidia Technologies, a New-Jersey based start-up has reinvented the cement mixture and curing process to cut CO2 emission by up to 70 percent. In order to make OPC (Ordinary Portland Cement), people mix limestone and sand with a ratio about 2/3 to 1/3. In Solidia, the mix ratio is about 50/50, and reaction happens at a much lower temperature around 1,200℃. This approach can cut 40% of CO2 emission, and uses 30% less energy to make the same amount of cement.
Solidia also injects CO2 into a drying chamber. As the cement hardens, the CO2 becomes trapped in the final concrete product. Such process also helps with water conservation by using CO2 instead of water during curing.
But for now, Solidia product can only be made in a controlled environment, which means they can only make small blocks instead of ready-mix concrete. The company has been doing test pours all around the United States, and working hard to make sure the new technology is recognised under the industry standards.
CEMENT-FREE CONCRETE
Dr. Gnanli Landrou was a doctoral student at ETH Zurich (Swiss Federal Institute of Technology in Zurich). Together with his mentor, they developed a process to turn clay-based excavation material into an alternative concrete without the addition of cement.
The team used purely natural materials, including the additives. The specific additive developed allowed the material to be able to harden within 24 hours but without cement.
Last year, they even started to develop the 2nd generation materials using all kind of waste, including construction waste, especially excavation materials from construction demolition.
Landrou’s soil-based concrete can be poured while fresh. It hardens rapidly and is suitable non-load-bearing walls. It’s not going to compete with traditional concrete since it is mostly suitable for 3 to 5-story houses or buildings. The product is considered 2.5 times cheaper, and 20 times eco-friendlier than conventional concrete.
Not too far away from Switzerland, a company in the U.K. uses by-product of other industries to make concrete. Cemfree is a totally cement-free alternative product developed by the DB Group back in 2015.
Cemfree uses ground-granulated blast furnace slag, which is a by-product of iron and steel making, to produce concrete. By removing cement, the patented system has significantly reduced the embedded CO2 in concrete. Cemfree also requires substantially less water than conventionally produced concrete.
All the above are just some examples from our desktop research. Even though we have so many alternatives, the Ordinary Portland Cement is still the cheapest, easiest to acquire, most-accepted material known to everyone. To change the status quo, all these alternatives still need to work on the product strength and cost. Can we trust the endurance of such products when facing extreme weather? Can monetary value be proven in real projects using these alternatives?
Meanwhile, it requires a culture shift. It would involve not only the cement factories, but also architects, engineers, real estates developers, and also investors. What can we do? We’re hoping that this article could serve as our first step to open our mind, and to get to know all the alternatives out there.
Again, don’t forget to Follow us on LikedIn, and share your thoughts with us.
Disclaimer: AvantFaire and its group companies have not invested in any of the companies and technologies mentioned in the article at the time of writing.
Reference List
- MIT Concrete Sustainability Hub Explained: Cement vs. concrete — their differences, and opportunities for sustainability
- Gates Notes: How to make concrete green.
- CNBC: This Green Cement Company Says It Can Cut Carbon Dioxide Emissions
- ETH Zürich: How Gnanli Landrou is closing the cycle
- The Guardian: David Ball Group invents cement-free concrete